Advantages of Wear-Resistant Steel (ABREX®) Vol.2~ “Processing precautions and heat resistance comparison ~
- Product
- ABREX
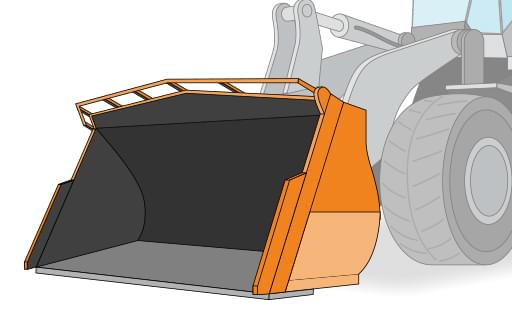
※)The content of this article reflects our views and is not guaranteed in its entirety. When purchasing or processing products, please consult with our company and other specialized professionals, and conduct appropriate verification based on the intended purpose and application before using the relevant material.
This blog is provided by Kumagai Speciality Steel, a specialist in special steels. It shares information about Japan’s high-performance steel materials in an easy-to-understand format, based on fundamental knowledge of special steels. Updates are made irregularly.
Table of Contents
・How is wear-resistant steel made?
・Types of wear
・Precautions when using wear-resistant steel
・Processing
・Cutting
・Welding
・Heat resistance of wear-resistant steel
・Impact wear resistance
How is wear-resistant steel made?
Not all details have been disclosed, but hardening through quenching is considered essential. Tempering may also be performed as needed.
In terms of composition, boron (B) is commonly added. Even in extremely small amounts, boron is a valuable element that enhances hardenability.Additionally, carbon (C) directly affects hardness. As hardness grades increase from 400 to 450 to 500, the regulated carbon range also rises, highlighting its importance. The martensitic structure formed by quenching steel is known to become harder in proportion to the carbon content.
When steel is quenched, the surface cools quickly, making it more likely to harden. If the plate thickness is thin, the entire material cools rapidly. However, in thicker plates, the cooling rate slows as you move inward, preventing sufficient hardening and making it difficult to achieve the desired hardness.
Therefore, as plate thickness increases, it becomes necessary to add elements that enhance hardenability. By adding these elements, the material can harden more easily even at slower cooling rates.
Elements that enhance hardenability include chromium (Cr), molybdenum (Mo), and nickel (Ni).
Adding these elements improves hardenability, but they are expensive. Additionally, as will be discussed later, they reduce weldability and increase susceptibility to cracking, making it necessary to balance their use. Steel manufacturers take these factors into account when determining the composition.
Types of wear
Types of wear include abrasive wear, where foreign particles scrape away the surface. Within this category, there is gouging wear, which occurs due to relatively large rocks cutting into the surface; grinding wear, where foreign particles get trapped between metals and are crushed, causing wear; and scratching wear, where small particles move along the surface, gradually wearing it down.1)
Wear-resistant steel like ABREX®, which has a uniform hardness throughout the matrix, provides consistent performance against various types of wear. However, some wear-resistant steels achieve their resistance by dispersing hard phases within the matrix, which may reduce effectiveness in cases such as gouging wear.
1)”Ichihara et al.: Construction Machinery 33 (1997), p. 52″
Precautions when using wear-resistant steel
・Processing
Regarding the machining of wear-resistant steel, such as cutting and drilling, its hardness makes processing more difficult.
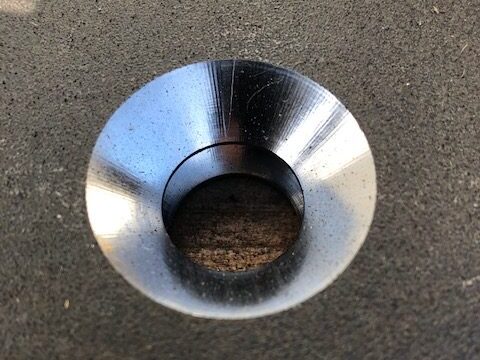
Wear-resistant steel is naturally more difficult to grind than general steel materials, but it can still be ground using a grinder. This is because the grinding wheel contains extremely hard materials such as alumina (approximately Hv1600) and silicon carbide (approximately Hv2400), which are significantly harder than wear-resistant steel (approximately Hv400–550).
Machining requires specialized tools that can withstand the hardness of the material. Since the material is hard, the tools must be even harder.
For drilling, if cobalt high-speed steel or powder high-speed steel is insufficient, cemented carbide may be required.
Optimizing cutting speed and feed rate is crucial. The same applies to milling. Selecting the appropriate tip (insert) and optimizing cutting speed and feed rate are essential. Please feel free to contact our company for further consultation on this matter.
・Bending
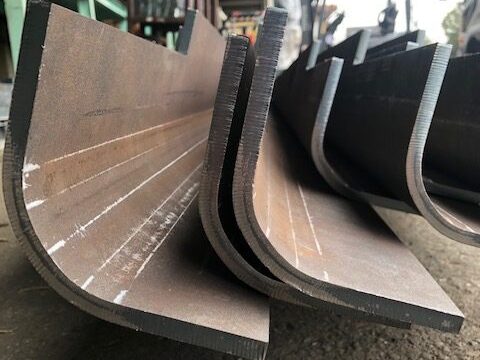
For bending, if you assume ABREX400 is equivalent to SS400 just because they both have a ‘400’ designation, you may experience excessive loading or, in some cases, cracking. Please be cautious.
Even with the same ‘400’ designation, hardness and tensile strength have different meanings.
The bending load required is approximately three to four times that of SS400. Additionally, sharp bends with a small radius are difficult, and it is necessary to secure several times the plate thickness.
Regarding bending direction, not only for wear-resistant steel but for steel plates in general, bending along the rolling direction (lengthwise) tends to be less prone to cracking compared to bending perpendicular to the rolling direction (widthwise).
Is this phenomenon similar to how a banana peel is easy to peel lengthwise but difficult to tear circumferentially? While the difference is not as extreme as with a banana peel, when performing bends close to the material’s limit, paying attention to the bending direction can help prevent cracking.
Additionally, if the bent edge of a component has been hardened due to cutting or other processes, cracks may originate from that area. Chamfering the tensile side during bending can help prevent crack formation.
・cutting of wear-resistant steel
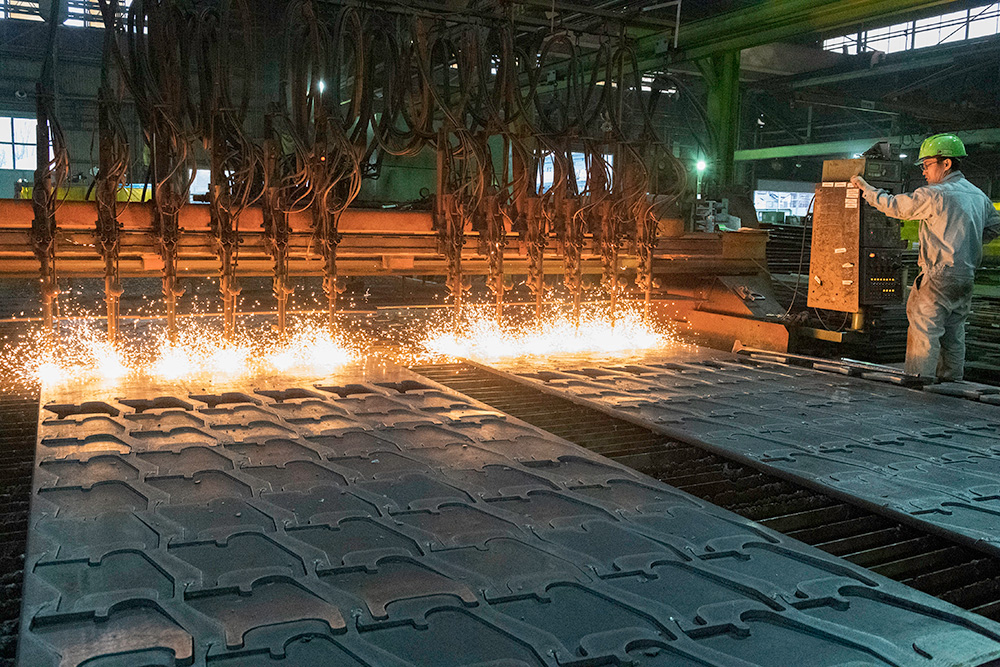
Wear-resistant steel is too hard for shear cutting, so the possible plate thickness is limited.
Even with band saw cutting, a standard saw blade quickly wears out and becomes unusable. If the blade is carefully selected, cutting with a saw is possible, but in general, thermal cutting is more commonly used since it is not affected by the hardness of the base material.
Wear-resistant steel has high hardness and contains a considerable amount of carbon, along with added alloys, making it more susceptible to cracking than general steel materials. In thermal cutting, such as gas cutting, the area near the molten zone undergoes rapid heating and cooling, resulting in re-hardening. If hydrogen penetrates the steel during gas cutting, cracks may appear after several tens of hours. Since these cracks do not occur immediately but develop over time, they are referred to as delayed cracking.
The gases used in cutting include propane (C₃H₈), acetylene (C₂H₂), and natural gas (mainly methane CH₄, among others). During combustion, carbon dioxide and water are produced, but a small amount of hydrogen atoms can penetrate the steel, which is said to contribute to cracking. The higher the hardness and the thicker the plate, the more prone it is to cracking.
Preheating before cutting is effective in preventing cracks. This is because it allows time for hydrogen in the steel to migrate and escape from the surface after cutting. In plasma cutting and laser cutting, unlike combustion gases, hydrogen penetration does not occur, reducing the risk of cutting-induced cracks. However, there is a limit to the plate thickness that can be cut.
Additionally, a tempered zone forms slightly on the base material side of the cut section, resulting in a softened area. In small components close to the cutting line, this softening reduces the effectiveness of the wear-resistant steel. In such cases, laser cutting and plasma cutting tend to create a narrower softened zone.
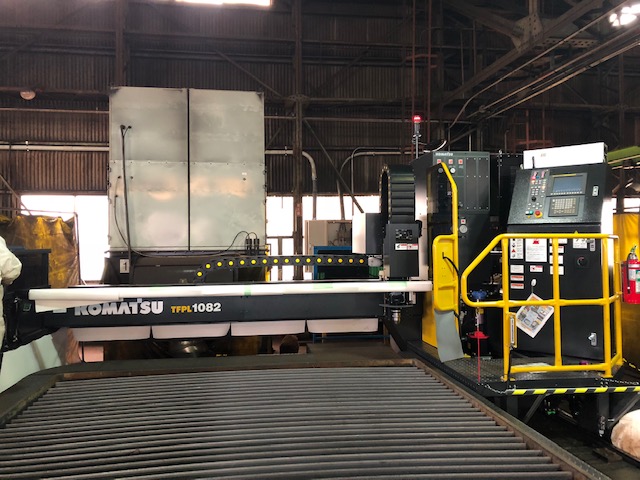
When performing continuous thermal cutting, the temperature of the base material gradually increases, so caution is required. To maintain the original hardness, it is said that the temperature should be controlled to stay below 200°C.
There are many precautions to take, making the process challenging, but they are necessary to maximize the properties of wear-resistant steel. If avoiding softening is prioritized over efficiency, in addition to the previously mentioned saw cutting, other methods include water jet cutting, which uses high-pressure water, and wire cutting, which utilizes electrical discharge machining.
・welding of wear-resistant steel
Given the significant constraints in cutting, one might assume that welding wear-resistant steel is extremely challenging. In some respects, this is true, but depending on how wear-resistant steel is used, welding may not pose as much of a problem in many cases.
Unlike high-tensile steel, wear-resistant steel is rarely used as a structural strength member, and the weld area is not often required to have the same hardness as the base material. However, if wear occurs primarily on the surface, excessive wear concentrated in the weld area can be problematic. In such cases, the weld must also have a certain level of hardness, and welding materials for 80-kg steel are sometimes used.
However, if the welded area is not exposed to significant wear because objects do not frequently come into contact with it, simply ensuring adhesion is sufficient. In such cases, mild steel welding materials can be used, making the welding process easier compared to welding 80-kg steel.
Welded areas are susceptible to residual stress from welding and hydrogen penetration, making them more prone to delayed cracking, as mentioned in the section on cutting. To prevent delayed cracking, common methods include using welding materials that minimize hydrogen absorption and preheating the steel before welding.
The preheating temperature varies depending on the composition, so it is advisable to consult a specialized company like ours or refer to the material manufacturer’s catalog each time.
In any case, exceeding 200°C tends to cause softening, so caution is necessary.
Additionally, in welding where all four sides are tightly constrained, residual stress increases, making cracking more likely. Special care is required, particularly for materials with high crack sensitivity, such as those in the Brinell hardness 500 class.
As a side note, delayed cracking can also occur due to corrosion, in addition to gas cutting and welding.
This type of cracking happens when prolonged exposure to moisture leads to corrosion, allowing hydrogen atoms to penetrate the steel. Since it develops after long-term use, corrosion prevention measures are necessary.
If the material gets wet but dries quickly afterward, there is no need for significant concern. However, avoid situations where rainwater seeps in and remains trapped without drying for an extended period.
Returning to the topic of welding, materials with relatively high strength and a large amount of alloying elements, such as high-tensile steel and wear-resistant steel, may become magnetized. This magnetism can distort the welding arc, making welding difficult. However, temporarily tack welding to create a short circuit can help reduce the impact.
There are also other techniques available, so feel free to consult us if you need assistance.
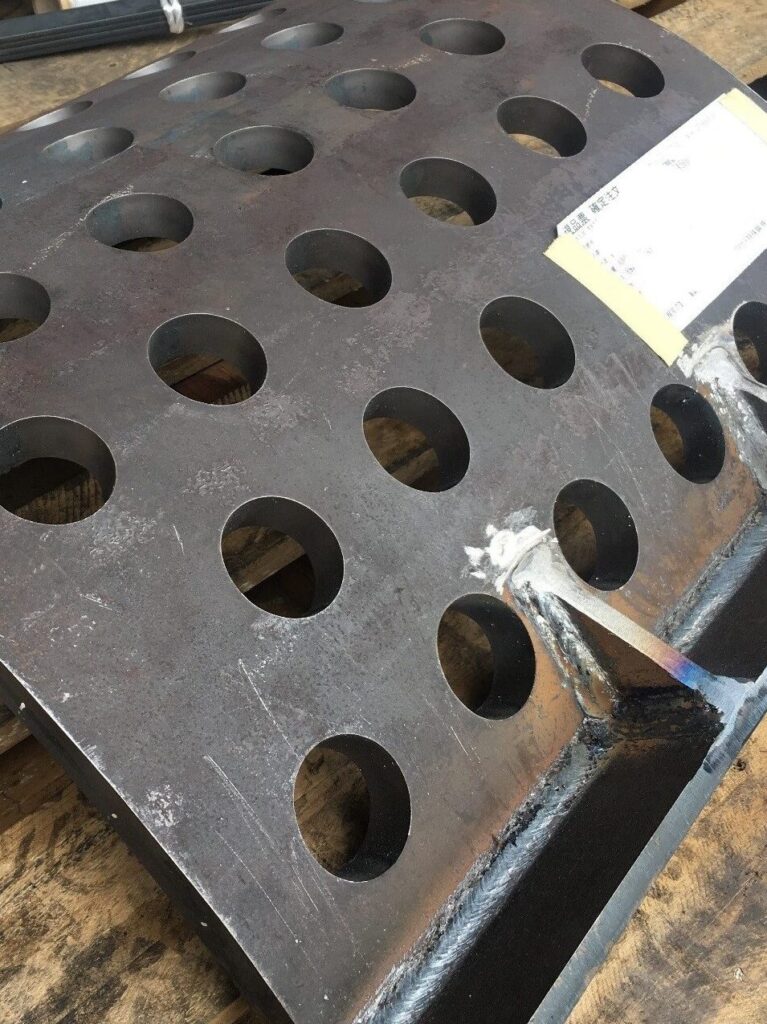
Heat resistance of wear-resistant steel
As previously mentioned, wear-resistant steel tends to soften as the temperature increases. While 200°C serves as a general reference point, the extent of softening above this temperature varies depending on its composition.
If you are experiencing wear issues at high temperatures of around 300°C to 400°C, please consult us. After reviewing the situation, we may be able to recommend suitable steel materials.
Impact wear resistance
In addition to wear-resistant steel, our company also handles high-manganese steel, which is impact-resistant and wear-resistant.
This steel material hardens upon impact from rocks, shot particles, or similar forces on the surface, effectively reducing wear.
Compared to general wear-resistant steel, it can provide significantly enhanced wear resistance depending on the application. A separate introduction to this steel material will be provided.
This concludes the explanation of wear-resistant steel. While there are various precautions to consider when using it, wear-resistant steel offers significant advantages, including a greatly extended replacement cycle and potential weight reduction. We highly recommend considering its use.
“Our company is…”
We are a specialized trading company based in Japan, dealing in high-tensile steel and other special steels.
Please feel free to contact us.
Feel free to email us.
↓↓↓
info@kumagai-steel.co.jp